JTEKT公司IoE概念的智慧型工廠
台灣機械工業同業公會 機械資訊
2019-11-21 11:04:04
加入我的收藏
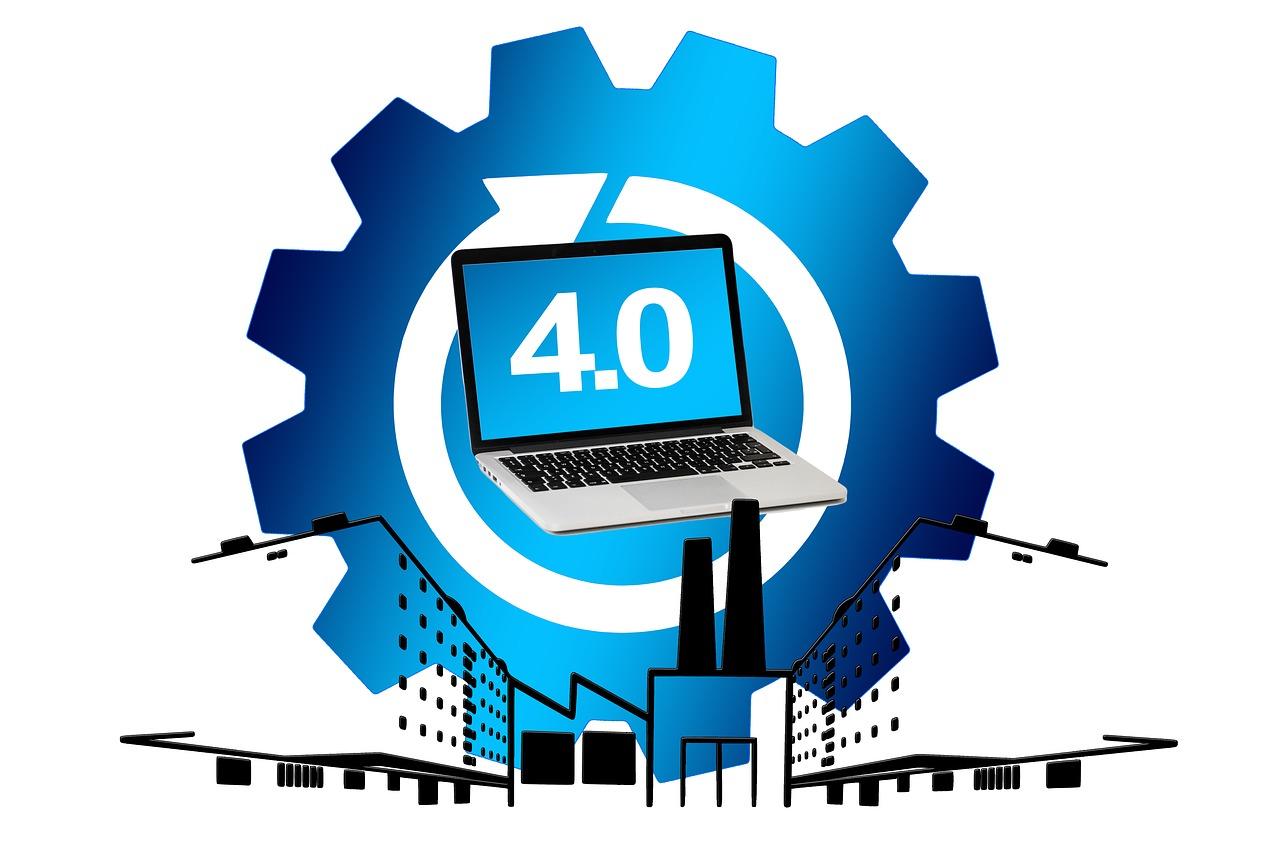
機械資訊 731期
翻譯/葉秀玲
大阪臺灣機械服務中心
因為工業4.0等的引進,加速了工廠邁向智慧化的動向。而JTEKT(捷太格特)的龜山廠也以「IoE」(萬物聯網)概念為基礎,透過獨家的設備取得不同環境下的數據,以求提升工廠的生產性。本篇將要為大家介紹龜山廠的組織架構。
許多公司對於活用IoT(物聯網)以及架構智慧型工廠,以提升工廠生產性能具有高度的興趣。雖然轉型為智慧型工廠尚存在著許多課題,其中最大的兩個課題為以下2項:「如何實踐『連結』」以及「人與機械之關連性」。
將這些定位明確化,並準備了各式各樣的技術來進行實證的正是JTEKT公司。接下來就要為大家介紹JTEKT公司如何引進「IoE」的架構以及龜山第2廠的實證。
輪殼組件生產順利的JTEKT龜山廠
JTEKT的龜山廠(三重縣龜山市)原本為製造深溝滾輪軸承、離合器軸承、內裝離合器的交流發電機等的工廠。之後因軸承生產體制重整之故,龜山廠接下原本由大阪柏原市國分廠製造的汽車用滾球輪殼組件。而為了因應新承接的工作,於是龜山廠新建造了第2廠房,於2016年完工。並慢慢搬入國分工廠的生產設備,開始進行生產。
之後,轉由龜山第2廠負責製造的汽車用輪殼組件需求增加,2015年的產能為600萬個,但到了2016年就擴大到700萬個。2017年的方針為提升到800萬個。然而,在有限的空間與生產設備的限制之下,為了可以提升產能,就必須從生產方式來著手下功夫。而JTEKT努力的方向就是活用IT系統,建構智慧型工廠。JTEKT將正在推行的「IoE系統」全面引進龜山第2廠,目標在於提升產能,並塑造一個可以成功實現「IoE」的案例。※)
※)相關記載:輪殼組件生產順利的JTEKT公司,預計增加輕型汽車的生產
以人為中心的「IoE」
擔任豐田汽車工廠生產線主要規劃要務的JTEKT公司,對於歐美所採用的工業4.0型智慧型工廠,因「看不到人的蹤跡」,而予以否定(JTEKT公司工具機、電機事業本部IoE推進室 第1組 組長 都築俊行先生)。都築組長認為:「製造始終應為人,且生產的技術也寄託在人的身上。即便要將工廠智慧化,也無需改變這點,還是必須以人為中心來提升工廠的生產性能或附加價值。」
基於上述的理念,JTEKT公司不使用「IoT」,不光只是「IoT」中的T(Thing:物)而已,加入了包含人這個要素的「IoE (Internet of Everything)」,並以此為概念,來推行工廠的智慧化。
JTEKT為了實現IoE的理念,將方向定位於下列四個步驟︰
1. 連結各個事物:連結
2. 連結各種資訊:可視化
3. 改善:收集資訊、分析、創造價值
4. 拓展範圍:共同分享數據
龜山到第2廠的全產線皆已實施到步驟2的「連結各種資訊(可視化)」。據說有部分的產線已經進入到了步驟3「改善」的實證階段。一般在實現智慧型工廠或IoT化時,最大的障礙就是「物的連結」這部分。因為工廠內運轉的機器,基本上都不是以「連結」為前提來製作。因此,各機器與設備所採用的資訊搜集方式與傳達方式也各不相同,數據就沒有辦法直接互相連結。如何吸收不同環境系統的差異,以實現數據的連結,就是實現智慧型工廠的一大課題。特別是老舊生產設備之大半都不具有通訊功能,因此就必須去尋找取得收集這類機台內數據的方法。同樣的問題也發生在龜山第2廠,龜山第2廠的許多設備都是自國分廠移轉過來,因此在這裡,也是新舊設備混雜的環境。
在新舊混合的環境中實現「連結化」
針對此課題,JTEKT展開了「JTEKT-LINK」※)。所謂「JTEKT-LINK」,是一個可以連接在既有設備上的系統,即使是其他公司的設備也能連接。這個系統除了可以進行既有設備與設備間的連結之外,也可進行設備的數據分析。此系統內部裝有PLC「TOYOPUC-Plus」,這是JTEKT所推展的系統,可以接續不同種類的Network,並可廣泛適用於Ethernet/IP、CC-Link、PROFINET或EtherCAT等各種Network。因為也可以使用I/O連結,因此即使是沒有Network的老舊設備也能連結。此外,這個系統不是加裝在既有的控制版上,而是附加(add-on)在設備的閒置處。
※)相關記載:既有設備智能化 JTEKT公司附加套組開賣
建立「可視化」的標準型
龜山第2廠,在輪殼組件研磨和組裝製程上,已用「JTEKT-LINK」將舊設備與新設備做連接。具有通訊功能(Ethernet Port:乙太網路端口)的設備能夠取得加工資訊、設備異常、生產實績、測定數據、運轉數據等資訊。即使是不具有通訊功能的設備,也可以取得設備停止的資訊及生產實績的資訊。將這些蒐集到的資訊集中到「PLC BOX」,以「線上安燈系統(Line-Andon)」來即時表示設備的運轉狀況,不論是誰都可以一眼就確認到發生異常的產線或設備。以往在確認那條產線故障因而造成中斷等問題點時,往往花太多時間,才使得損失擴大。因為可視化了,所以能及時把握到發生異常的產線或設備,馬上就可以收集到即使的狀態。結果就是能夠避免大停機。
為了讓人眼能立刻就了解到設備的運轉狀況,因此工廠中安裝了許多安燈系統,可以即時掌握到設備的運轉資訊。同時,將這些收集到的資訊,也顯示於作業人員附近所安裝的「操作盒」上。從這個「操作盒」上可以看到品質資訊的變更、一定時間點的數據顯示或是交出資料等作業。透過「操作盒」,作業人員可以一面作業,一面確認整體產線的情形及相關零件產線的狀況。甚至可以在平板或智慧型手機上確認這些資訊。
JTEKT龜山第2廠在進行「IoE化」的同時,也努力改善產線的配置與作業環境等,因此無法將『IoE化』的成果完全區分出來(都築氏)。但綜合這些生產性能等努力改善的成果,相較於從前的國分廠,龜山第2廠工程內工具機數量減少了40%,電力消耗量也減少了30%。
用安裝感應器的預防保全來實證步驟3
JTEKT龜山第2廠目前已經實現了步驟1的「連結」及步驟2的「可視化」。目前正持續推動進入步驟3「改善」的階段。也就是裝有感應器的設備,以達到預防保全的效果。
在龜山第2廠4號產線的研磨設備上,安裝了一部光洋電子製造的「OnSin Sensor」。這是可以測量溫度和3軸加速度狀況的感應器。在預測保全的實證中,將感應器所感應到的數據記錄在數據紀錄器中。記錄到的內容會透過無線網路傳輸到邊緣型分析模組「TOYOPUC-AAA」中,並擷取資訊記錄於伺服器中。
都築說:「一旦等到研磨材等材料磨耗而損壞時,光是更換或保養維修就必須讓產線暫停約5小時左右。若能夠確實掌握到震動或溫度等數據,就可以掌握到損壞的前兆,就可以利用在沒有作業的時期,計畫性的更換零件。這樣一來就可以控制對作業效率的影響。若要提升預測故障的精準度,就必須蒐集更多的數據,如果可以蒐集到更多的數據,就可以提升預測的精準度,並在適當的時機進行零件的更換。」
JTEKT將這個引進IoE概念的輪殼組件研磨產線,作為JTEKT集團內部有關輪殼組件生產的示範產線。這也就是「全球標準產線(GSL)」的其中之一,並且提出了擴展到世界各工廠的方針。雖然時程尚未確定,但據說在增設產線計畫中的墨西哥、印尼、東歐等,已列入安裝的方針。
品質、保全、生產的IoE
JTEKT今後推動的方針,包括將現場的技術與IT融合,持續進行以現場為中心的智慧型工廠。此計畫的內容包括了下述三項,目的就是要利用這三個重點讓解決對策更加進化,其中包括:製品品質徵兆管理的「品質的IoE」、壽命或異常徵兆管理的「保全的IoE」、實現可以提升包括人與機器設備生產性能的「生產的IoE」。
都築接著說:「目前引進IoE的工廠除了這所提到的龜山廠,另外總公司的刈谷工廠及香川的香川工廠也在進行推動計劃。目前刈谷工廠的數據伺服器已準備好,將持續推動工廠進入步驟4的『連鎖解決方案』。刈谷工場、香川工廠與龜山廠目前都已連結起來。三個工廠就像是一個工廠一樣,可以一次就掌握到所有工廠的狀況。」
資料來源:MONOist,http://monoist.atmarkit.co.jp/mn/articles/1705/24/news041.html
翻譯/葉秀玲
大阪臺灣機械服務中心
因為工業4.0等的引進,加速了工廠邁向智慧化的動向。而JTEKT(捷太格特)的龜山廠也以「IoE」(萬物聯網)概念為基礎,透過獨家的設備取得不同環境下的數據,以求提升工廠的生產性。本篇將要為大家介紹龜山廠的組織架構。
許多公司對於活用IoT(物聯網)以及架構智慧型工廠,以提升工廠生產性能具有高度的興趣。雖然轉型為智慧型工廠尚存在著許多課題,其中最大的兩個課題為以下2項:「如何實踐『連結』」以及「人與機械之關連性」。
將這些定位明確化,並準備了各式各樣的技術來進行實證的正是JTEKT公司。接下來就要為大家介紹JTEKT公司如何引進「IoE」的架構以及龜山第2廠的實證。
輪殼組件生產順利的JTEKT龜山廠
JTEKT的龜山廠(三重縣龜山市)原本為製造深溝滾輪軸承、離合器軸承、內裝離合器的交流發電機等的工廠。之後因軸承生產體制重整之故,龜山廠接下原本由大阪柏原市國分廠製造的汽車用滾球輪殼組件。而為了因應新承接的工作,於是龜山廠新建造了第2廠房,於2016年完工。並慢慢搬入國分工廠的生產設備,開始進行生產。
之後,轉由龜山第2廠負責製造的汽車用輪殼組件需求增加,2015年的產能為600萬個,但到了2016年就擴大到700萬個。2017年的方針為提升到800萬個。然而,在有限的空間與生產設備的限制之下,為了可以提升產能,就必須從生產方式來著手下功夫。而JTEKT努力的方向就是活用IT系統,建構智慧型工廠。JTEKT將正在推行的「IoE系統」全面引進龜山第2廠,目標在於提升產能,並塑造一個可以成功實現「IoE」的案例。※)
※)相關記載:輪殼組件生產順利的JTEKT公司,預計增加輕型汽車的生產
以人為中心的「IoE」
擔任豐田汽車工廠生產線主要規劃要務的JTEKT公司,對於歐美所採用的工業4.0型智慧型工廠,因「看不到人的蹤跡」,而予以否定(JTEKT公司工具機、電機事業本部IoE推進室 第1組 組長 都築俊行先生)。都築組長認為:「製造始終應為人,且生產的技術也寄託在人的身上。即便要將工廠智慧化,也無需改變這點,還是必須以人為中心來提升工廠的生產性能或附加價值。」
基於上述的理念,JTEKT公司不使用「IoT」,不光只是「IoT」中的T(Thing:物)而已,加入了包含人這個要素的「IoE (Internet of Everything)」,並以此為概念,來推行工廠的智慧化。
JTEKT為了實現IoE的理念,將方向定位於下列四個步驟︰
1. 連結各個事物:連結
2. 連結各種資訊:可視化
3. 改善:收集資訊、分析、創造價值
4. 拓展範圍:共同分享數據
龜山到第2廠的全產線皆已實施到步驟2的「連結各種資訊(可視化)」。據說有部分的產線已經進入到了步驟3「改善」的實證階段。一般在實現智慧型工廠或IoT化時,最大的障礙就是「物的連結」這部分。因為工廠內運轉的機器,基本上都不是以「連結」為前提來製作。因此,各機器與設備所採用的資訊搜集方式與傳達方式也各不相同,數據就沒有辦法直接互相連結。如何吸收不同環境系統的差異,以實現數據的連結,就是實現智慧型工廠的一大課題。特別是老舊生產設備之大半都不具有通訊功能,因此就必須去尋找取得收集這類機台內數據的方法。同樣的問題也發生在龜山第2廠,龜山第2廠的許多設備都是自國分廠移轉過來,因此在這裡,也是新舊設備混雜的環境。
在新舊混合的環境中實現「連結化」
針對此課題,JTEKT展開了「JTEKT-LINK」※)。所謂「JTEKT-LINK」,是一個可以連接在既有設備上的系統,即使是其他公司的設備也能連接。這個系統除了可以進行既有設備與設備間的連結之外,也可進行設備的數據分析。此系統內部裝有PLC「TOYOPUC-Plus」,這是JTEKT所推展的系統,可以接續不同種類的Network,並可廣泛適用於Ethernet/IP、CC-Link、PROFINET或EtherCAT等各種Network。因為也可以使用I/O連結,因此即使是沒有Network的老舊設備也能連結。此外,這個系統不是加裝在既有的控制版上,而是附加(add-on)在設備的閒置處。
※)相關記載:既有設備智能化 JTEKT公司附加套組開賣
建立「可視化」的標準型
龜山第2廠,在輪殼組件研磨和組裝製程上,已用「JTEKT-LINK」將舊設備與新設備做連接。具有通訊功能(Ethernet Port:乙太網路端口)的設備能夠取得加工資訊、設備異常、生產實績、測定數據、運轉數據等資訊。即使是不具有通訊功能的設備,也可以取得設備停止的資訊及生產實績的資訊。將這些蒐集到的資訊集中到「PLC BOX」,以「線上安燈系統(Line-Andon)」來即時表示設備的運轉狀況,不論是誰都可以一眼就確認到發生異常的產線或設備。以往在確認那條產線故障因而造成中斷等問題點時,往往花太多時間,才使得損失擴大。因為可視化了,所以能及時把握到發生異常的產線或設備,馬上就可以收集到即使的狀態。結果就是能夠避免大停機。
為了讓人眼能立刻就了解到設備的運轉狀況,因此工廠中安裝了許多安燈系統,可以即時掌握到設備的運轉資訊。同時,將這些收集到的資訊,也顯示於作業人員附近所安裝的「操作盒」上。從這個「操作盒」上可以看到品質資訊的變更、一定時間點的數據顯示或是交出資料等作業。透過「操作盒」,作業人員可以一面作業,一面確認整體產線的情形及相關零件產線的狀況。甚至可以在平板或智慧型手機上確認這些資訊。
JTEKT龜山第2廠在進行「IoE化」的同時,也努力改善產線的配置與作業環境等,因此無法將『IoE化』的成果完全區分出來(都築氏)。但綜合這些生產性能等努力改善的成果,相較於從前的國分廠,龜山第2廠工程內工具機數量減少了40%,電力消耗量也減少了30%。
用安裝感應器的預防保全來實證步驟3
JTEKT龜山第2廠目前已經實現了步驟1的「連結」及步驟2的「可視化」。目前正持續推動進入步驟3「改善」的階段。也就是裝有感應器的設備,以達到預防保全的效果。
在龜山第2廠4號產線的研磨設備上,安裝了一部光洋電子製造的「OnSin Sensor」。這是可以測量溫度和3軸加速度狀況的感應器。在預測保全的實證中,將感應器所感應到的數據記錄在數據紀錄器中。記錄到的內容會透過無線網路傳輸到邊緣型分析模組「TOYOPUC-AAA」中,並擷取資訊記錄於伺服器中。
都築說:「一旦等到研磨材等材料磨耗而損壞時,光是更換或保養維修就必須讓產線暫停約5小時左右。若能夠確實掌握到震動或溫度等數據,就可以掌握到損壞的前兆,就可以利用在沒有作業的時期,計畫性的更換零件。這樣一來就可以控制對作業效率的影響。若要提升預測故障的精準度,就必須蒐集更多的數據,如果可以蒐集到更多的數據,就可以提升預測的精準度,並在適當的時機進行零件的更換。」
JTEKT將這個引進IoE概念的輪殼組件研磨產線,作為JTEKT集團內部有關輪殼組件生產的示範產線。這也就是「全球標準產線(GSL)」的其中之一,並且提出了擴展到世界各工廠的方針。雖然時程尚未確定,但據說在增設產線計畫中的墨西哥、印尼、東歐等,已列入安裝的方針。
品質、保全、生產的IoE
JTEKT今後推動的方針,包括將現場的技術與IT融合,持續進行以現場為中心的智慧型工廠。此計畫的內容包括了下述三項,目的就是要利用這三個重點讓解決對策更加進化,其中包括:製品品質徵兆管理的「品質的IoE」、壽命或異常徵兆管理的「保全的IoE」、實現可以提升包括人與機器設備生產性能的「生產的IoE」。
都築接著說:「目前引進IoE的工廠除了這所提到的龜山廠,另外總公司的刈谷工廠及香川的香川工廠也在進行推動計劃。目前刈谷工廠的數據伺服器已準備好,將持續推動工廠進入步驟4的『連鎖解決方案』。刈谷工場、香川工廠與龜山廠目前都已連結起來。三個工廠就像是一個工廠一樣,可以一次就掌握到所有工廠的狀況。」
資料來源:MONOist,http://monoist.atmarkit.co.jp/mn/articles/1705/24/news041.html