提高生產效率的最新技術
台灣機械工業同業公會 機械資訊
2019-11-21 11:05:21
加入我的收藏
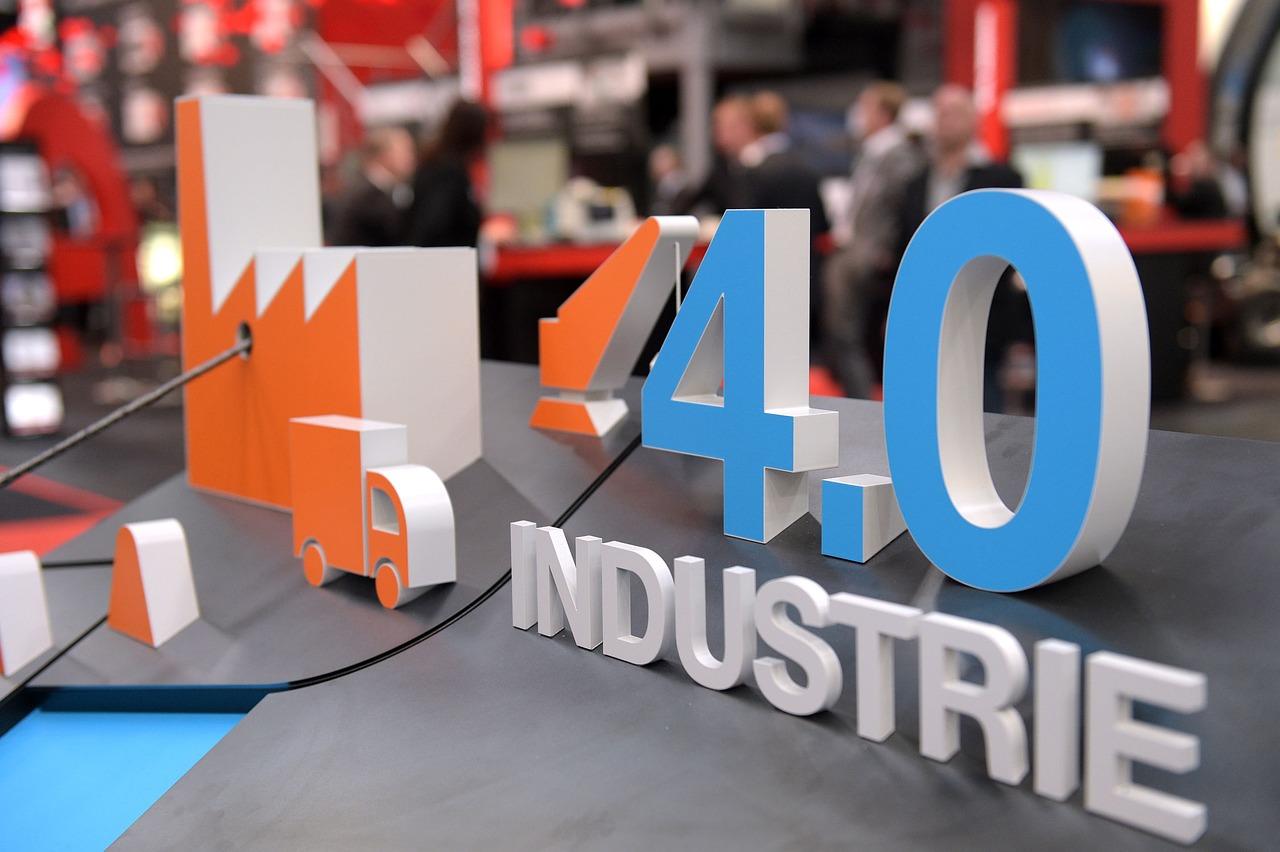
機械資訊 740期
翻譯/林意珊
大阪臺灣機械服務中心
邁向更有生產性的未來。
工具和工具機的傳感器速度控制,隨著概念具體化的進展,成為一個大趨勢。
Sensing a More Productive Future.
Sensor-Based Control of cutting Tools, Machine Tools Moves From Drawing Board to Mainstream.
Robert Puhr (Manufacturing Engineering、 Contributing Editor)
致力於工業4.0和工業物聯網IIoT等成功的主要原因之一,是許多優秀的傳感器被整合到綜合加工機以及工具本身。這些傳感器的數據和連接性是實現"Factory of the Future(未來工廠)"的基礎。
另一方面,雖然不能說是未來或是接下來的事,但目前可以利用的“智慧傳感器”也可以看到有各種發展。可以收集數據、並通知操作人員機器和加工過程的狀態。像這樣的發展也已經實現,更精確地測量零件的位置和加工工件的幾何形狀,是為了可以設定和管理加工中使用的工具。
因此,本雜誌Manufacturing Engineering聽取業界多數專家的意見,並調查傳感器速度的加工控制系統的現狀。以及預測其未來的可能性。
■目前、展望未來
傳感器速度控制的優化領域是,以從制定概念的階段到成熟產品的道路來比喻的話,是從哪個地方過來的?「不同的地方」,除了這樣的回答以外似乎沒有其他說法。
Marposs Corp公司(密西根州奧本山)的研磨相關產品的Manager-Frank Powell說:「關於基本測量和自適應控制,我們整齊地遵循學習曲線」。「在工具機上可安裝各種各樣的加工用傳感器和換能器。達到基本程度,這種傳感器用於機器維護上。工具機系統的話,對於可能會有無法預期的負載和衝突,會比操作人員的反應快1,000倍。這個技術正在穩定的發展中。可以更精確地測量零件的位置並測量提升零件的幾何形狀,並且還可以設置和管理用於加工的工具。從工業4.0的角度來看,如果說工具的數位技術是一個成熟的產品,倒不如說是制定概念階段這樣來比較恰當。
Sandvik Coromant公司(紐澤西州菲爾朗)與『Silent Tool』相關的技術營業專家Neil Munson說:從工業4.0的角度來看,如果說工具的數位技術是一個成熟的產品,倒不如說是制定概念階段這樣來比較恰當。「現在這個行業正處於模式轉變,事實上我們正在實現基於傳感器的智慧工具的第一次躍進。」
另一方面,BadAxe-Tooling Solutions公司的Joe yolansky先生有一些不同的看法。「該產品銷售上有許多實績,並且經常遵循學習曲線。就我們公司而言,可以說這是一個週期性的步驟,我們基於紮實的科學知識發售適用銑削加工的產品。為擴展機器的物理運動提供了一種全新的解決方案」。Bad Axe Tooling Solutions是一家企業聯盟,由美國的Briney ToolingSystems公司(密西根州BadAxe)、Fullerton Tool公司(密西根州薩基諾)和BlueSwarf LLC公司(賓夕法尼亞州州學院)的這三家公司所組成。
Okuma America Corp集團(北卡羅來納州夏洛特市)產品技術和技術中心的Manager-Wade Anderson說道:「以我的角度來看,開發方面正處於學習曲線的中間位置」、「基本的機器效率與相關機器的通訊功能,已經有許多購買後可立即使用的現成解決方案。然而,人工智慧(AI)和擴增實境(AR)技術還有其他的可能性」。
現在,生產現場的機器設備正在生產大量數據。Anderson指出,這項技術具有如此新的可能性,Praemo公司(加拿大 安大略省基秦拿)技術事務的統括責任者Andy Henderson表示:「自動化的領域中,1970年代以後很顯然地是“物質的”演變。下一個開發領域將是活用AI和機器學習(ML)進行數據智慧的“精神的”演變。AI和ML的技術穩步成熟並繼續用於個人和商業領域(Google、Amazon 和Facebook等,更是不可或缺的。)製造業中的應用雖然遲了一些,但利用這種技術的『Razor』等軟體,在加工現場也開始能夠實際感受到Al和ML的價值。」Henderson先生這麼說。Praemo的產品『Razor』連接數據資源收集資訊並顯示狀態。此外,透過減少機器設備停機時間和優化生產流程,我們提供建議,讓使用者可以採取預防措施進行風險管理。
■決定因素是傳感器
業界的專家也一致認為,傳感器是一個重要的角色。「只要目標可以被測量,那麼他就可以被管理〔What Gets Measured Gets Managed〕」,有這麼樣的一個格言,是誰說的已不可考(有說法是物理學家凱爾文男爵,也有一說是經營學家彼得‧德魯克),其主要觀點是,任何控制或優化設備的嘗試都是一個重要的接觸點。也就是說,它是基於工具和工件接觸點的快速且準確的可靠數據。
就技術面來說,熟練收集 分配 分析用於自適應控制數據的技術,早在像現今的工業4.0和工業物聯網IIoT獲得注目之前,就已經可以利用。從歷史上看,加工過程中的測量設備的根源,可以追溯到60年以上(例如,由Marposs公司的創始人Mario Possati用於檢查磨削零件的量規等)然而,直到最近傳感器才取得了重大進展。
■最新技術
像這樣的進展之一,是一種自動修正切削刀具磨損的鑽頭。「無論數控工具機如何複雜,都無法自動補正鑽頭的尖端磨損」Rigibore Inc公司(威斯康辛州馬闊納戈)社長Anthony Bassett表示:「我們公司的『ActiveEdge』工具透過電池驅動自動進行鑽頭刀片的加工過程中尺寸調整。使用無線通訊技術遙控調整一個工具上多個切削刃的外徑,以優化過程的性能。無需操作人員干預。」
此外,『BadAxe Smart Tool』工具和軟體系統正在開闢銑刀加工領域的新領域。根據BadAxe的說法,可以從一開始就立即掌握機器的“最佳位置”,而無需實際反覆試驗(圖1)。對於加工機械和主軸、刀塔、刀具的組合使用固有頻率模式的測量值來執行分析,採用專利技術演算法分析並且計算對於加工機器的操作最佳的穩定區域。從結果來看,除了即用型平衡刀架和刀具組件外,還提供了針對每台加工機械的優化軟體界面。
BadAxe公司的Volansky表示:「眾所周知,振動和顫振是高速加工的主要限制因素。因此,操作人員通常重複嘗試以找到合適的進給、切割速度、切割幅度、切割深度等。據說材料去除率非常大。實際上,有可能在與直覺相反的條件下不進行振動,我們擔心在許多情況下的有效性。對於我們公司的產品,無論是表面處理、凹槽加工、角加工等,都可以從一開始就立即確定這樣的加工條件。由Boeing公司的研發部門Phantom Works和美國國防部等證實,其背後的技術可以顯著提高投資回報率(ROI)。
BadAxe已經在各種工具機和工具的組合上建立了一個大型數據資料庫。如果數據資料庫中沒有客戶的工具機,則可以執行附加測試以確定該條件下的動態特性。
同時,Sandvik Coromant公司Munson表示:透過導入智慧工具『Silent Tools+』將其傳感器從“過程”中更改為“工具”中。「『Silent Tools+』具有作為工具的振動控制功能,為操作人員通常依賴於直覺而進行超出的長加工處理,提供了絕佳的預測。」
「先進的設備很難處理超出的加工,因為操作人員需要管理所有過程到工具的先端為止。因此,我們在『Silent Tools』內部建構了一個傳感器,並通過藍牙與圖形界面進行通訊,使其覆蓋機器並在成為深孔內搜索的操作人員的“眼睛”和“耳朵”(圖2)。此外,它還具有判斷切削刃是否位於中心的功能,並且可以輕鬆快速地進行設置。
使用這種『Silent Tools+』系統,可以實際監控工具的偏轉和振動、切削阻力、刀具負載、溫度。Munson說:「因為可以掌握這類資訊,我們相信它會提高產量並提高生產力,也可帶來實際的節約。」
■更多的資訊
對於僅用於獲得數據的傳感器,如果可以處理傳感器的信號並將其用於品質管理和工具狀態管理上,則可產生附加價值。製造商的話可以縮短加工過程及時間、改善成品、延長機械使用壽命,還可以有效地處理複雜形狀和薄壁空心圓柱形零件和細長軸零件等困難的工件。
Okuma公司的Anderson如下說道:「作為第一步『Okuma Monitoring System』是很好的。根據每個過程的要求,最多可以定制64個輸入。對於我們的客戶,客戶可以測量機器停機時間並分析綜合設施效率OEE數據,簡單來說,當操作人員無法從別處離開時的情況下,機器會停止運轉。因此,如果使用監控系統,操作人員會收到可能出現問題的警告,並可採取預防措施予以預防。
臺灣塑橡膠機械廠商多為中小企業,無論是生產或銷售,都能展現高度彈性,快速因應環境變化,再加上完整的產業聚落、具競爭力的價格,深受全球買主肯定,造就臺灣塑橡膠機械2017年出口值超過11億美元的佳績。
另一方面,Praemo公司的Henderson先生認為,為了在生產中取得成功,最終要突破處理應用程序中工具所產生的大量數據。「這些數據是用於優化的“原始數據”。我們公司的『Razor』軟體分析數據的算法可以篩選大量數據並發現相互關係和模式。這是在電子表格軟體中絕對找不到的資訊。此外,使用人工智慧Al(Artificial Intelligence)和機械學習ML(Machine Learning)技術開發模型,以便操作人員和管理人員可以做出快速及明確的判斷,並根據他們的數據驅動類型的判斷進行應對。
雖然這些知識是人工的,但非常接近製造領域的人們如何處理事情的判斷。唯一的區別是,即使數據龐大也不需要擔心。隨著收集更龐大的數據,將可學習到許多關於『Razor』的知識」。
■能力已實際證明
Marposs公司的Powell先生表示,現今的系統已經證明了能夠維持加工過程的能力,例如可預期問題的發生、告知操作人員和對機器採取糾正措施。「僅由用戶決定是只有通知還是做出自動應對,技術上有很多自動控制的可能性,但有些情況下還是沒有充分被利用」。
Marposs公司所提供名為『BLU』的新系統中,有超過50年的磨床等工具機的生產經驗。所有機器監控和過程控制的應用程序都集成在一個系統中,透過高速採樣和數據處理進行工具和實際加工的監控和自適應控制,以及緩和衝突。根據Powell先生的說法,「『BLU』旨在與工具機緊密整合,以在所有情況下,例如在設置、手動操作、自動駕駛等過程中協助操作人員。
系統的核心是主節點,可以包含在機器的控制面板中。它有一個總線結構,允許插入節點並可以連接其他節點,這些節點具有透過在線測量儀器測量的值、音射AE(Acoustic Emission)監控、(磨床上)砂輪的平衡、工具縮回運動等功能。
其他還有像是Rigibore公司的『Zenith』系統,Bassett先生說,這是一個用於鑽孔加工的閉環自動化系統。「傳統系統只是一個機械系統,從未對鏜刀加工機進行持續反饋。針對這個部分,『Zenith』向機器的控制裝置提供反饋,並且可以確認工具是否已經調整了預定量。來自該位置傳感器的反饋可防止不良品被加工。」圖3:Rigibore公司的『Zenith』作為與加工機器控制裝置連接的閉環系統,自動確認鑽孔工具是否已經調整了預定量。
■這些技術可以使用多久?
Sandvik Coromant公司的Munson先生說:「無法確認數據解決方案和傳感器速度控制最終會使用多久。然而,即使在最新的加工現場和生產設施中,適用消費者的產品應用程序所走的路徑,在未來五到十年內,工具傳感器和工業物聯網IIoT的活用也會更為常見。」「即使是我們公司,將數控工具機和『Silent Tools+』控制統合在一起也是很自然的。但現在它是一個可即時顯示過程狀態的獨立系統,工具機製造商和CAM軟體的夥伴企業合作,我們正進行將這個獨立系統朝向機器控制和加工過程的整合發展」。
Okuma公司的Anderson先生也這麼想。「技術,最重要的是它的實際應用,來培育新的技術。雖然是很久以前的事了,在我看來,汽車的自動防眩光鏡對我來說沒什麼,但現在我不會想購買沒有附加自動防眩光鏡的汽車。在機器加工業界也是,新的技術將會促成推動新市場的進一步發展」。
Marposs公司的Powell先生也認為遊戲永遠不會結束。「用於監控各種關鍵參數和變量的技術已經到位,但肯定還有部分可以改進。因此,我們每天都致力於開發更快速且精準的傳感器,以及可以更敏捷快速地處理傳感器數據的軟體。在這10年當中,我認為毫無疑問,至少會出現一種作為改變遊戲規則的完全創新技術。這是一項技術突破,進一步提高了機械加工現場的效率和生產性。如果遊戲發生變化,我們公司將會相應改變」。
另一方面,Bad Axe公司的Volansky先生只是將公司視為改變遊戲規則的公司。他說:「發展速度越來越快,客戶不會等待5年或10年。我們公司有幫助工具機操作人員面臨物理上限制的產品,以及重塑效率概念的產品。儘管如此,我們目標也是下一階段。透過將專利技術的振動測量功能和數據處理功能結合到工具機及其控制邏輯操作中,可以將我們的模具零組件與困難問題區隔開來」。另外他也提到,若是這樣,可以的話時常可以在優化到極高水準的狀態下操作工具機,並且不需要操作人員的反覆試驗。
Rigibore公司的Bassett先生也談到:「我們的發展目標,為了減少操作人員干預,包括使用CNC控制設備自動訂購硬質合金刀具、從中心的一個地方進行調整,並且即使在執行其他過程時也可以將實體模型輸入到CNC工具機中。但是,現在最大的障礙是,不同的數控工具機製造商和控制設備製造商之間沒有兼容性,而且規格很少。結論來說,Bassett先生認為,即使採用自己的方法,發展也會受到限制,對於想要輕鬆添加新功能的客戶來說,最終成本將會很高。
Praemo公司的Henderson先生表示,有人說遊戲的最後階段是完全的自動生產,沒有任何人為的干預。但是「就個人而言,完全自動化的實現,就像是追求世界和平一樣。對製造業來說,這是一個能夠努力的價值、有魅力的理想,但考慮到很多情況則無法實現。然而,內置傳感器的工具或工具網絡,使用軟體來整合收集合計 分析數據,如果將工具機與工廠的資訊資源組織化的話,這樣可以說是非常接近一個完全自動化的工廠。這並不是說機器取代了人。說到底是單純的將作業人員從勞動中解放,增加了更多的滿足感,最終實現高度生產率。類似於CNC的登場。經數控的工具機手動操作已經自動化,任何人都知道可以安全的作業,提高生產率」。
資料來源:機械與工具,2018年8月號,頁A22~A26。