工具機智慧化技術動向 —工程設計的自動化及切削加工的活用
台灣機械工業同業公會 機械資訊
2019-11-21 11:04:35
加入我的收藏
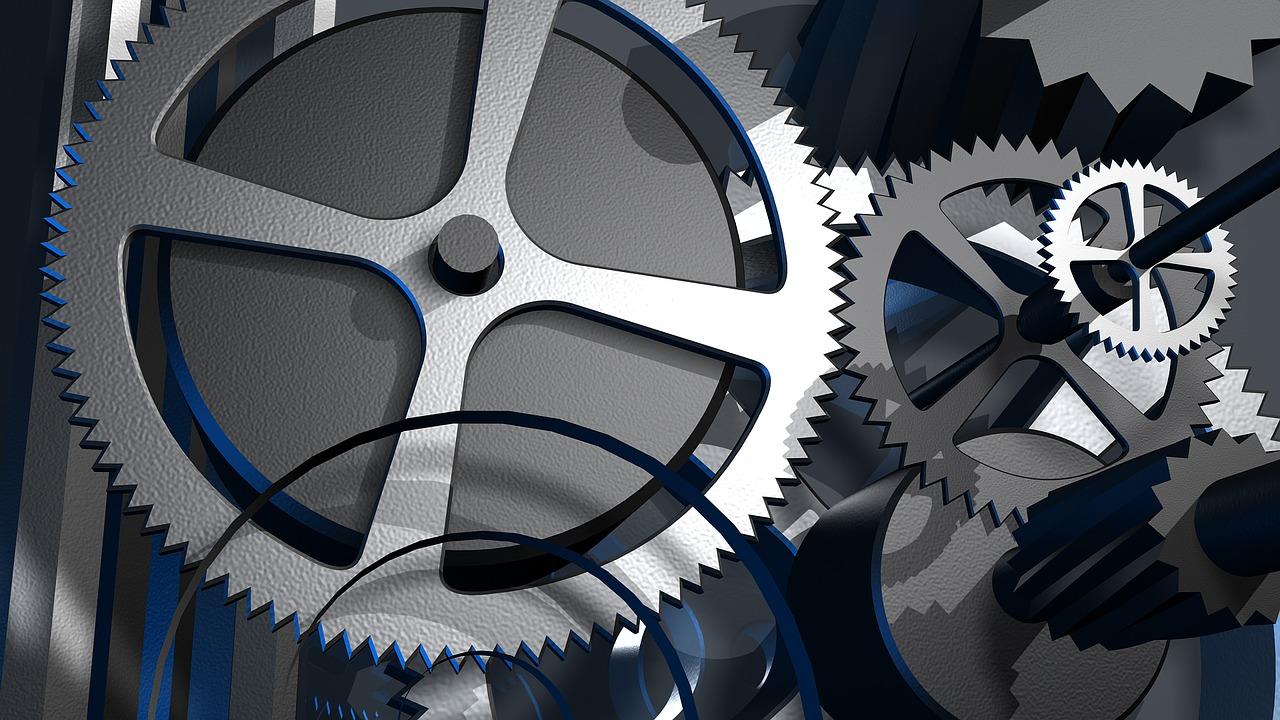
機械資訊 733期
作者/白瀨 敬一
翻譯/蔡淑芬 大阪臺灣機械服務中心
1.前言
雲端電腦(Cloud Computer)、物聯網(IoT)、人工智慧(AI)、深度學習(Deep Learning)等成為熱門話題時,在製造業中,只要提到德國的工業4.0(Industry 4.0)、美國的工業網際網路聯盟ICC (Industrial Internet Consortium),焦點便著重在物聯網智慧製造(smart manufacturing)。在日本機器人革命主導權(Initiative)協議會、產業價值鏈主導權(Industrial Value Chain Initiative)企業聯盟中,也正朝向實現智慧製造(Smart Manufacturing)努力中。
另外,日本提倡的社會5.0 (Society 5.0)中,定義了超智慧社會的實現目標,「對必要的人,在必要的時候,提供必要的商品及服務,可以對應社會中各式各樣細微的需要,包括提高對人服務的品質,超越年齡、性別、地區、言語等各種差異的限制,讓這個社會可以變得更有朝氣及更讓人快意生活的社會。 」
但是,在日本的製造業中,因為少子化及高齡化的問題,使得直接面臨了從業人員的減少、以及熟練技能者的退休等窘境。然而,在工業產品的製造中,生產形式從大量生產到單品生產(客製化生產),產品壽命相對變得比較短,零件的形狀、加工過程也變得相對繁雜。如圖1所示,機械加工用的NC程式NC Program的製作,其中自動化設置的勞力一直在增加,但設置的人力資源卻仍然在減少。由於人力資源的不足,也影響到自動化的實現。為了補救人力資源不足的問題,也要致力於從工具機到生產設備的高度智慧化及自主化的實現。
2.以NC程式(NC program)作為機械加工指令的問題點
在機械加工的自動化中,如圖2所示的步驟,雖然是以NC程式完成機械加工,但是NC程式只能輸入工具機的動作指令,而無法傳達工具機加工產品的設計資訊、加工資訊等相關訊息。因此,以現行的NC程式作為機械加工指令,有以下難以解決的問題。
(1) 因為無法傳達工具機加工產品的設計資訊、加工資訊等相關訊息,也限制了智慧化及自主化的達成。舉例來說,NC程式在接收到亮麗光滑的加工指令後進行加工,但不是設計完成的加工形狀指令,所以NC程式便只能用推估的方式進行產品形狀的加工。又加上不清楚加工產品所使用的材料、使用的刀具等,使得工具機對加工狀況無法清楚地掌握。
(2) 因為是以NC程式作成的時間點決定工具機的使用,所以無法直接改變工具機的使用來做生產計畫的變更。
(3) 因為是以NC程式作成的時間點決定工具機的使用,所以在刀具還沒有準備好之前是無法進行加工。
(4) 因為是以NC程式作成的時間點決定切削條件、刀具加工的流程,所以也無法使得加工狀況的切削條件優化、控制加工流程等。
3.透過CAD/CAM/CNC的合作帶動工具機智慧化及自主化
為了解決上述目前所存在的問題,有關加工產品的設計資訊、加工資訊等達到工具機需求是很重要的。可以達到這個目的的方法是經由CAD/CAM/CNC的合作,如圖3所示為資訊傳達的流程圖。
和現行的方式最大的不同是,①工具機可以知道加工產品的設計資訊、加工資訊。②透過CAM和CNC的合作,工具機的軸配置、動態特性考量刀具加工流程。由於在現行的方式下,刀具加工流程的決定,無法將工具機的軸配置、動態特性考量進來,CNC可以先讀取刀具加工流程訊息,以便回避急速的加速或減速。另外並非預先給予刀具加工流程的指令,但如果可以在加工過程中,逐步給予刀具加工流程的指令,如此亦能對應加工狀況,使得有優化的切削條件、及控制加工的流程等,這樣便能完全實現新智慧化及自主化功能了。
筆者基於以上的考量,進行有關工具機的刀具加工流程計算、控制加工流程,及實現可能的自主型、智慧型NC工具機的研究。
這個創新的工具機已被日本內閣府主導的策略性創新創造計畫(SIP)/創新性設計生產技術所採納,研究開發專案為“CAM/CNC整合之創新性工具機的智慧化及機械加工技術的高度化”。如圖4所示,為以實用化為目標的試用工具機的配置。圖中的數位仿形銑床DCM(Digital Copy Milling)的操作加工的重點是一邊複製實物模型,一邊控制工具機的動作,在要開始進行加工產品的CAD模型之仿形加工的同時,在過程中計算出刀具路徑。當將產品和材料的CAD模型訊息傳給工具機後,便可以輕易地如3D列印一樣進行產品加工,而無需事先準備NC程式。
工具機加工的步驟為:①產品模型的選擇、②工作模式的選擇、③工程設計、④加工開始,在這4個步驟中,加工中的CNC畫面及加工實例如圖5所示。相關的動畫可連結以下網址:https://www.youtube.com/watch?v=rz5TNkONRS
這個試用機在2015年的EMO、2016年的IMTS、JIMTOF中展示過。
4.反映加工技巧(know-how)的工程設計之自動化
筆者在上述自主化、智慧化NC工具機的研究中,採用了工程設計的自動化。如果可以實現工程設計的自動化,便能自動完成NC程式(NC Program)的加工程式。即使是使用目前的NC工具機,也可能讓NC加工程式的工作量減少。然而,若採用傳統的程式演算(Algorithm)達到工程設計的自動化,技術人員想要的加工順序、想決定的切削條件等,可能會有困難。也就是說,程式演算即使可以達到某個技術人員的想法,但可能無法讓工程設計的結果多樣化,要讓其他技術人員也滿意的加工順序、或不能決定切削條件等問題,便成為重要的課題。因此,目前挑戰的是透過技術人員對CAM操作的過程相關資料的收集、累積,分析各操作者的加工技巧,學習工程設計並反映在自動化。
加工順序如圖6所示,由材料形狀、產品形狀的3次元CAD模型算出的加工除去領域,將其分割得到的各加工領域之圖示。加工順序的決定著重在各加工領域的“加工特徵(Feature)”(機械加工特有的形狀特徵)。技術員依照以往的CAM操作學習經驗決定各個加工特徵(Feature)的加工順序。另外,即使是決定好了加工特徵(Feature),技術員也會依自己學習到的技巧,包括加工特徵(Feature)的幾何學相關資料的收集,對收集後資料的分析判斷,例如決定大體積的加工順序、由右到左的順序等,這就是所謂技術員的加工技巧學習。學習後的經驗,依照加工特徵(Feature)的優先順序、幾何學等資料,如圖7所示決定加工工程形式流程,從中也反映出技術員在各加工領域的加工技巧,也自動產生其中的加工順序。這種方法的特色是不必詢問技術員加工工程設計的目的及方針,而是從CAM的操作履歷中學習加工的技巧,這種可以反應學習結果的加工工程設計,相當具有多樣性及柔軟性。
加工順序決定後,依據加工特徵(Feature)決定加工條件。加工條件是技術員依照過去操作CAM的NC程式(NC program)時,決定後的加工特徵(Feature)所使用的刀具、刀具路徑、切削條件等加工條件,累積成為加工案例資料庫。因此,可以在資料庫找尋加工特徵(Feature),包括位置、體積、形狀等幾何學相關的資料,以符合和類似新加工案例的加工特徵(Feature)。如圖8所示,找出最符合新加工案例的加工特徵(Feature),如此便能有最合適的加工條件,也能自動決定出其加工條件。如上所述,可以自動決定加工順序及加工條件,是利用了CAM功能中NC程式(NC program)自動作成的功能。
5.模擬切削加工的應用
以NC程式作為機械加工指令的問題點,在前述文章中舉出了工具機無法掌握的加工狀況。工具機為了能夠掌握加工狀況,以加工產品的形狀、材質、使用中的刀具等資料為基礎,應用模擬切削加工可以得到效果。工具機的衝突回避技術,可以利用模擬的過程中找出衝突,若可以進一步善用模擬切削加工,依據模擬的結果作為判斷加工狀況的適當與否、適應性控制等,便能達到工具機高度智慧化。
筆者也以掌握工具機加工狀況的方法,正在開發以端銑刀(end mill)加工為主的模擬切削加工。此模擬切削加工中,加工物是適用立體模型(Voxel model),以端銑刀(end mill)刀片切除立體模型所檢測出的加工形狀變化,同時加上計算的結果,根據不斷變化的切削厚度計算加工過程中的切削力和切削扭力(torque)。立體模型是將3D形狀表示為微小立方體的模型,這需要大量的記憶體才能表現出物體形狀的細節,但另一方面,此模型也具有可以表現形狀及處理形狀的特點。
切削加工模擬器的執行畫面如圖9所示,在這個案例中,圖形左側表示的是具有凹槽及小洞的加工物經由端銑刀(end mill)加工時的形狀變化,以及在圖形右側是隨著時間變化的計算得到的切削力圖表。
接下來,將以加工異常檢測及適應性控制作為模擬活用實例。如圖10所示為加工異常檢測,是以切削加工模擬器計算切削扭力(Torque),並和主軸馬達扭力相比較後,判斷有無加工異常。隨著使用刀具、切削條件、加工狀況的變化,若只以主軸馬達扭力大小(臨界值的設定),做為加工異常有無的判斷是有困難的,但如果透過模擬的結果,因為可以提供對應的使用刀具、切削條件、加工狀況變化等判斷基準,所以加工異常檢出的判斷就變得容易了。
適應性控制如圖11所示,經由切削加工模擬器計算所得到的切削扭力及切削力可以維持恆定,因此可以用來做適應性控制。適應性控制之所以不普及,是因為在工具機上安裝測量切削力的動力計是不實際的,但如果是使用模擬結果,就不需要安裝動力計。在圖11為假想模仿加工系統(DCM)及組合構造圖,若以NC程式先進行模擬加工,即使是目前的NC工具機也可以做到適應性控制,如此便可以避免因為超載引起的刀具損壞的加工故障問題。
6.高度切削加工模擬之實現
筆者雖然長久以來一直進行端銑刀(end mill)加工的切削加工模擬的研究,但為了能更了解加工現象,需要有更高度的模擬技術支援。在上述所介紹的切削加工模擬是刀具為剛體(不變形)的前提下靜態切削力的預測。筆者目前開發的立體模型的切削加工模擬器,如圖12所示,透過切削加工模擬的多目的、多用途利用,擴展了使用功能,使得可以用更小的立體進行動態分析。透過降低空間分辨和時間分辨率的情況下進行動態分析時,如圖13所示,出現在加工表面的切削痕跡和表面粗糙度,可以分析加工過程中的振動現象。
到目前為止的切削加工模擬中,是透過刀具與切削物的關係來預測切削力,但加工時的切削力是作用於工具機的結構上、刀具進給驅動系統及主軸驅動系統。但由於工具機的振動、刀具進給速度、主軸迴轉數等是會隨時變動,因此必須要有能夠考量這些相互作用的切削加工模擬技術。
筆者在圖14所表示的是,把可以進行動態分析的切削力模型、能夠表現工具機和刀具進給驅動系統的工具機模型、以及可以表現主軸驅動系統動態特性的主軸驅動系統模型,整合進行了組合模擬。組合模擬中,刀具刀片的軌跡,(1)計算切削力模型中的切削扭力(Torque)及切削力。(2)計算工具機模型中的刀具及切削物的相對位置,進一步再計算主軸驅動系統模型中的刀具迴轉角度,其中每隔一小段時間交互重覆計算(1)和(2)。因此,考慮到切削力對刀具的動態運動的影響,及刀具的動態運動對切削力的影響,此兩者的組合效果可以用來預測切削力。
切削力的測量結果及組合模擬的結果,在不考慮工具機、驅動系統的動態特性的切削力模擬結果如圖15所示的比較圖。結果顯示的是重切削加工條件的案例,因為工具機振動及切削力的交互作用,明顯產生切削力波形的混亂。本文章中介紹的高度切削加工模擬,對於加工中切削力的混亂、異常振動發生原因的探討、異常振動的抑制方法、以及工具機的構造、控制系統的設計方式的探討等,可以提供幫助。
7.結語
工業4.0的目標是追求在智慧工廠中可能達到高度智慧化及自主化,如工具機可以自己決定加工工程及加工條件。但是,以現行的NC程式作為機械加工指令,因為無法傳達工具機加工產品的設計資訊、加工資訊等相關訊息,以致於工具機的智慧化及自主化也受到了限制。文章中所提到的CAD/CAM/CNC的合作,是工具機在加工過程中,可以將設計資訊、加工資訊等加以應用,使加工品質可以得到控制的重要概念。此外,應用工程設計的自動化、切削加工模擬,可以彌補生產現場人力資源不足的問題,如此也成為可以實現工具機的智慧化及自主化的關鍵。