航太新興表面處理技術發展趨勢
經濟部技術處
2021-01-06 15:40:36
加入我的收藏
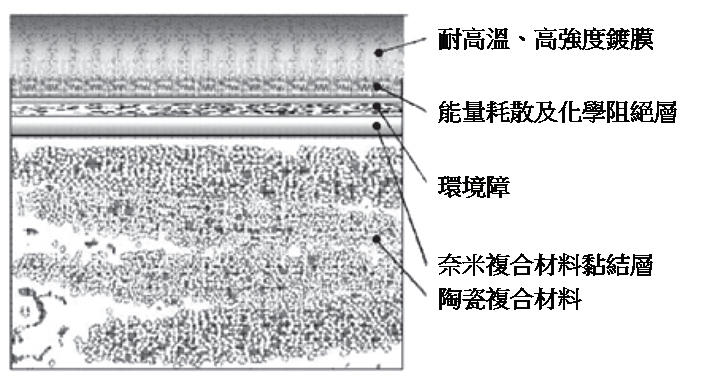
發表日期:2021-01-06
作者:陳仲宜(金屬中心)
摘要:
根據2018年波音公司所發表的商用飛機市場展望指出,預測全球未來20年內將交付4.27萬架新機,產值達6.3兆美元,帶動航空系統及零組件市場龐大商機。航太工業快速發展,對產品及零組件的抗氧化、抗腐蝕、抗磨損、耐熱、抗疲勞及特殊功能等性能有著越來越高的要求。
全文:
一、前言
根據2018年波音公司所發表的商用飛機市場展望指出,預測全球未來20年內將交付4.27萬架新機,產值達6.3兆美元,帶動航空系統及零組件市場龐大商機。航太工業快速發展,對產品及零組件的抗氧化、抗腐蝕、抗磨損、耐熱、抗疲勞及特殊功能等性能有著越來越高的要求。單一的材料往往無法滿足高性能航空設備的使用要求,而表面處理技術可以非常有效地彌補材料性能的不足,使其適應嚴苛的工作條件。鍍膜材料與鍍膜製備關鍵技術的掌握與創新對延長產品使用壽命、降低能源消耗、提升產品可靠性具有重要意義。時值我國政府正積極輔導廠商投入開發航太關鍵技術能量、建立航空品質系統及特殊製程認證,藉由推動航太產業聚落,共同打造臺灣航空產業優質供應鏈,並與全球航空大廠接軌,成為亞太地區航空產業重要合作夥伴。因此,本文擬探討航太設備及零組件未來應用需求之新興表面處理技術發展趨勢,作為相關業者在技術佈局的參考。
二、航太新興鍍膜技術發展動向
目前快速發展中的航空表面處理技術包括高性能熱障鍍膜(Thermal barrier coatings,TBCs)、超高溫複合材料零組件表面環境障鍍膜(Environmental barrier coatings,EBC)、高溫可磨耗密封鍍膜、WC-Co及氧化鋁鈦等耐磨鍍層、吸波及紅外隱身鍍膜等技術,鍍膜的應用大幅提高航空產品的性能、可靠性、經濟性、服役壽命及戰機的生存能力。
(一)新型高性能熱障鍍膜
熱障鍍膜通常應用於航空引擎高壓渦輪葉片表面,對葉片基體發揮隔熱防護與延壽作用,主要是由隔熱性能優良的陶瓷面層與具黏接作用的金屬底層所構成,可以避免高溫燃氣與金屬基體直接接觸,對基體形成有效保護,發揮延長引擎工作壽命、提高燃燒效率的作用,已經成為現代航空引擎高壓渦輪葉片三大關鍵製造技術之一。目前應用最廣泛的熱阻障鍍膜製備技術是大氣電漿噴塗(Air plasma spray,APS)及電子束物理氣相沉積(Electron beam physical vapor deposition,EB-PVD)技術。
電漿噴塗物理氣相沉積(Plasma spray-physical vapor deposition,PS-PVD)是一種最近發展的功能薄膜製備技術。該技術結合電漿噴塗與物理氣相沉積兩種技術的特點,代表未來高性能熱障鍍膜製備技術的發展方向。與前二者相比較,PS-PVD用快速熱噴塗的方法實現大面積、均勻化的物理氣相沉積。透過改變電漿射流狀態,PS-PVD 還可以實現多相複合膜層的沉積,拓展不同組織結構熱障鍍膜的設計與製備。更為重要的是,PS-PVD 的電漿射流具有良好的繞鍍性,可以在外形複雜的工件表面實現非直視性熱障鍍膜沉積。總體來說,PS-PVD 工法有望在新一代超高溫、高隔熱、長壽命熱障鍍膜研製方面發揮關鍵作用。
(二)高溫複合材料表面環境障鍍膜
環境障鍍膜是確保複合材料構件在航空引擎中長時間服役的關鍵,主要用來抵抗環境的腐蝕,同時還兼具阻斷及癒合裂紋與空隙的作用。因此,環境障鍍膜材料的選擇必須滿足以下四個基本條件。
1. 必須具備良好的抗氧化腐蝕能力,同時還需具備較低的氧擴散率;
2. 熱膨脹係數必須與基體材料相匹配,以避免在熱循環過程中因熱應力導致的裂紋及分層,甚至剝落;
3. 在使用溫度範圍內必須具有良好熱穩定性,意即不發生相變;
4. 與基體材料不發生任何有害的化學反應,意即與基體具有良好的化學相容性。
環境障鍍膜材料體系大致經歷四個階段:第一代-莫來石與氧化釔穩定氧化鋯(Mullite/YSZ)系統;第二代-鋇鍶鋁矽酸鹽(Barium strontium aluminosilicate,BSAS,Ba1-xSrxAl2Si2O8,0≤x≤1)系統;第三代-稀土矽酸鹽(Rare-earth(RE) silicates,RE:稀土元素)體系;第四代-熱/環境障鍍膜(Thermal/Environmental barrier coatings,T/EBC)系統。
第三代環境障鍍膜已基本滿足1,400℃燃氣環境中的長期使用,但是著眼於未來複合材料的發展與應用,NASA結合在高溫合金上使用的熱障鍍膜,提出熱/環境障鍍膜的設計理念,以滿足碳化矽/碳化矽襯裡及葉片未來在1,650℃水氧耦合環境中的使用要求。其塗層結構設計如【圖1】所示,主要結構包括四層。第一層是表層耐高溫的熱障鍍膜,主要由具有低導熱率的陶瓷材料組成,包括La2Zr2O7及Gd2Zr2O7等,為下面膜層及基體提供絕熱防護,同時能夠作為第一級輻射遮罩層,以減少來自於高溫燃燒室環境及膜層高溫表面的紅外熱輻射;第二層是能量消耗層及化學阻絕層;第三層是環境阻絕層;第四層是奈米複合材料黏結層。
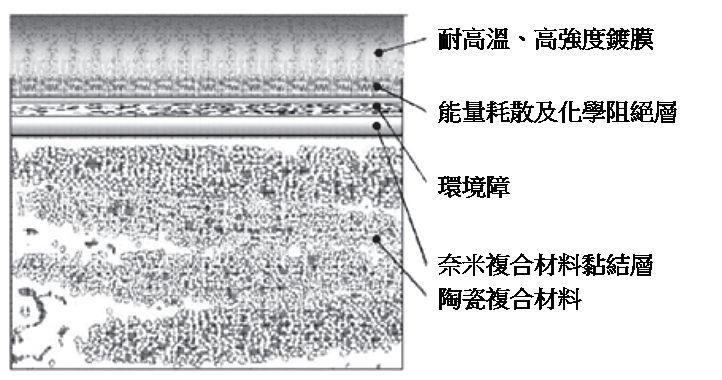
資料來源:Ceramic Transactions /金屬中心MII-ITIS研究團隊整理
圖1 1,650℃條件下使用的先進T/EBC設計原理
(三)高溫可磨耗密封鍍膜
隨著能源危機加劇,提高引擎效率、降低油耗成為目前航空引擎的研發焦點之一。為提高引擎效率,保護葉片與機匣不受刮擦損傷,在航空發動機氣路密封的設計與開發中導入「可磨耗」密封鍍膜,以維持最小氣路間隙而提高引擎性能。高溫可磨耗密封鍍膜用於引擎渦輪氣路密封,可減小渦輪葉片葉尖與渦輪外環之間的間隙,進而減少氣體洩漏、提高引擎效率。一般設計要求在渦輪葉片與密封鍍膜發生接觸刮擦時,膜層被刮削而葉片磨損甚小,並且摩擦係數要小,以免刮擦產生的高溫造成鍍膜或葉片燒蝕開裂,因此高溫可磨耗密封鍍膜需具有一定的減摩功能。一般來說,金屬基可磨耗密封鍍膜抗氣流沖蝕性能優良,而氧化物陶瓷基可磨耗密封鍍膜抗氣流沖蝕能力相對較差,因此在材料組成及鍍膜製備工法參數控制方面必須予以高度關注,以保證鍍膜使用壽命。
近年來,電漿噴塗MCrAlY高溫合金型(如NiCrAlY、CoCrAlY、NiCrAlYSi等)可磨耗密封鍍膜及陶瓷基(如稀土氧化物穩定ZrO2、A12O3等)可磨耗密封鍍膜獲致明顯進展,膜層可磨耗性能及抗沖蝕性能明顯提高。MCrAlY具有高溫抗氧化及抗熱腐蝕作用,一般添加聚苯酯作為造孔劑,聚苯酯加熱去除後在膜層內留下大量細小均勻分佈的孔隙可以降低膜層硬度、增加膜層可磨耗性、減輕膜層對渦輪葉片的磨損。添加六方BN或氟化物作為減摩自潤滑材料,降低摩擦係數。高溫可磨耗密封鍍膜厚度一般超過1.5mm,必須採用機器人自動噴塗技術,噴塗參數電腦閉迴路控制、鍍膜厚度線上監測,如此才能保證鍍膜組織結構及厚度的均勻性與再現性。
(四)熱噴塗陶瓷膜代替硬鉻電鍍層
因電鍍硬鉻對環境有持久的危險性,電鍍廢液中的六價鉻更是嚴重危害人體健康,減少直至取消電鍍硬鉻工法意義重大。近年來超音速火焰噴塗(High velocity oxygen fuel或High velocity air fuel,HVOF或HVAF)WC-Co、WC-Co-Cr、Cr3C2-NiCr金屬陶瓷鍍膜、電漿噴塗Cr2O3及A12O3-TiO2氧化物陶瓷鍍膜在工業上獲得廣泛應用,全面取代電鍍硬鉻工法已是必然。高速火焰噴塗WC-Co-Cr鍍膜在空巴、波音、洛克希德-馬丁等生產的先進軍/商用飛機(包括空巴A380、波音787、F-35等)已成功應用,結果顯示高速火焰噴塗的WC-Co-Cr2鍍膜在耐磨、防腐蝕、抗疲勞等關鍵性能指標明顯優於傳統硬鉻電鍍層。Cr3C2-NiCr鍍膜廣泛用於高溫摩擦磨損環境,渦輪導葉密封採用高速火焰噴塗Cr3C2-NiCr硬質鍍膜(主動磨削鍍膜)或電漿噴塗A12O3-TiO2陶瓷硬質鍍膜,具有耐蝕、高溫抗氧化、耐磨損等能力。電漿噴塗Cr2O3陶瓷硬質鍍膜在引擎密封及飛機運轉零組件磨損防護方面應用廣泛,其耐磨性及防蝕性較傳統硬鉻電鍍層提高數倍。
(五)奈米鍍膜
奈米材料技術是在1980年代誕生並仍快速發展的新技術,受到世界各國高度重視。物理氣相沉積(PVD)、化學氣相沉積(CVD)、熱噴塗、分子束磊晶(MBE)、化學沉積、電沉積等方法是獲得奈米鍍層或薄膜的典型方法。近10年來研究人員利用PVD(包括磁控濺射、離子束濺射、射頻放電離子鍍、電漿離子鍍、EB-PVD等)在製備奈米單層膜及奈米多層膜方面獲致很多成果,如奈米Ti(N,C,CN)、(V,Al,Ti、Nb、Cr)N、SiC、β-C3N4、α-Si3N4、TiN/CrN、TiN/A1N、WC-Co鍍膜可用於飛機軸類零件耐磨防蝕;電漿噴塗奈米A1203-TiO2鍍膜已用於航空引擎氣路密封;奈米Y2O3-ZrO2鍍膜已用於渦輪葉片隔熱防護;添加石墨烯、碳奈米管複合鍍膜具有雷達隱身功能。
熱噴塗是製作奈米鍍膜的極有競爭力的方法之一,與其他技術相比,具有許多優越性,如工法簡單、鍍膜材料及基體選擇範圍廣、可製備厚膜、沉積速率高、膜層成分易控制、容易形成複合功能鍍膜等,適用於大型零組件。採用奈米團聚粉末作為熱噴塗餵料,藉由嚴格控制工法參數,縮短奈米材料在焰流中的停留時間、限制原子擴散及晶粒長大,可製備奈米鍍膜。
三、未來展望
根據日本飛機協會的調查指出,由於新興國家客戶需求強勁及貨運量增加,全球商用飛機市場的年成長率為5%。與此同時,對飛機的需求亦逐年增加,預計在未來20年內將增加約兩倍。每架飛機約由300萬個零組件所組裝而成,由此可知,為滿足此一量產需求,表面處理在航空產業應用需求不可小覷。此外,根據歐盟委員會(European commission)數據,飛機排放溫室氣體,約佔全球溫室氣體4%,目前還在持續成長中。歐盟的目標是希望到2050年,飛機每公里二氧化碳排放量減少60%、氮氧化物污染減少90%、噪音減少75%。為達成此一目標,飛機製造商勢必更積極導入新興材料及關鍵零組件,而勢必將進一步推升相對應之新興表面處理技術的需求。
(本文作者為金屬中心執行產業技術基磐研究與知識服務計畫產業分析師)
全文連結:https://www.moea.gov.tw/MNS/doit/industrytech/IndustryTech.aspx?menu_id=13545&it_id=342
作者:陳仲宜(金屬中心)
摘要:
根據2018年波音公司所發表的商用飛機市場展望指出,預測全球未來20年內將交付4.27萬架新機,產值達6.3兆美元,帶動航空系統及零組件市場龐大商機。航太工業快速發展,對產品及零組件的抗氧化、抗腐蝕、抗磨損、耐熱、抗疲勞及特殊功能等性能有著越來越高的要求。
全文:
一、前言
根據2018年波音公司所發表的商用飛機市場展望指出,預測全球未來20年內將交付4.27萬架新機,產值達6.3兆美元,帶動航空系統及零組件市場龐大商機。航太工業快速發展,對產品及零組件的抗氧化、抗腐蝕、抗磨損、耐熱、抗疲勞及特殊功能等性能有著越來越高的要求。單一的材料往往無法滿足高性能航空設備的使用要求,而表面處理技術可以非常有效地彌補材料性能的不足,使其適應嚴苛的工作條件。鍍膜材料與鍍膜製備關鍵技術的掌握與創新對延長產品使用壽命、降低能源消耗、提升產品可靠性具有重要意義。時值我國政府正積極輔導廠商投入開發航太關鍵技術能量、建立航空品質系統及特殊製程認證,藉由推動航太產業聚落,共同打造臺灣航空產業優質供應鏈,並與全球航空大廠接軌,成為亞太地區航空產業重要合作夥伴。因此,本文擬探討航太設備及零組件未來應用需求之新興表面處理技術發展趨勢,作為相關業者在技術佈局的參考。
二、航太新興鍍膜技術發展動向
目前快速發展中的航空表面處理技術包括高性能熱障鍍膜(Thermal barrier coatings,TBCs)、超高溫複合材料零組件表面環境障鍍膜(Environmental barrier coatings,EBC)、高溫可磨耗密封鍍膜、WC-Co及氧化鋁鈦等耐磨鍍層、吸波及紅外隱身鍍膜等技術,鍍膜的應用大幅提高航空產品的性能、可靠性、經濟性、服役壽命及戰機的生存能力。
(一)新型高性能熱障鍍膜
熱障鍍膜通常應用於航空引擎高壓渦輪葉片表面,對葉片基體發揮隔熱防護與延壽作用,主要是由隔熱性能優良的陶瓷面層與具黏接作用的金屬底層所構成,可以避免高溫燃氣與金屬基體直接接觸,對基體形成有效保護,發揮延長引擎工作壽命、提高燃燒效率的作用,已經成為現代航空引擎高壓渦輪葉片三大關鍵製造技術之一。目前應用最廣泛的熱阻障鍍膜製備技術是大氣電漿噴塗(Air plasma spray,APS)及電子束物理氣相沉積(Electron beam physical vapor deposition,EB-PVD)技術。
電漿噴塗物理氣相沉積(Plasma spray-physical vapor deposition,PS-PVD)是一種最近發展的功能薄膜製備技術。該技術結合電漿噴塗與物理氣相沉積兩種技術的特點,代表未來高性能熱障鍍膜製備技術的發展方向。與前二者相比較,PS-PVD用快速熱噴塗的方法實現大面積、均勻化的物理氣相沉積。透過改變電漿射流狀態,PS-PVD 還可以實現多相複合膜層的沉積,拓展不同組織結構熱障鍍膜的設計與製備。更為重要的是,PS-PVD 的電漿射流具有良好的繞鍍性,可以在外形複雜的工件表面實現非直視性熱障鍍膜沉積。總體來說,PS-PVD 工法有望在新一代超高溫、高隔熱、長壽命熱障鍍膜研製方面發揮關鍵作用。
(二)高溫複合材料表面環境障鍍膜
環境障鍍膜是確保複合材料構件在航空引擎中長時間服役的關鍵,主要用來抵抗環境的腐蝕,同時還兼具阻斷及癒合裂紋與空隙的作用。因此,環境障鍍膜材料的選擇必須滿足以下四個基本條件。
1. 必須具備良好的抗氧化腐蝕能力,同時還需具備較低的氧擴散率;
2. 熱膨脹係數必須與基體材料相匹配,以避免在熱循環過程中因熱應力導致的裂紋及分層,甚至剝落;
3. 在使用溫度範圍內必須具有良好熱穩定性,意即不發生相變;
4. 與基體材料不發生任何有害的化學反應,意即與基體具有良好的化學相容性。
環境障鍍膜材料體系大致經歷四個階段:第一代-莫來石與氧化釔穩定氧化鋯(Mullite/YSZ)系統;第二代-鋇鍶鋁矽酸鹽(Barium strontium aluminosilicate,BSAS,Ba1-xSrxAl2Si2O8,0≤x≤1)系統;第三代-稀土矽酸鹽(Rare-earth(RE) silicates,RE:稀土元素)體系;第四代-熱/環境障鍍膜(Thermal/Environmental barrier coatings,T/EBC)系統。
第三代環境障鍍膜已基本滿足1,400℃燃氣環境中的長期使用,但是著眼於未來複合材料的發展與應用,NASA結合在高溫合金上使用的熱障鍍膜,提出熱/環境障鍍膜的設計理念,以滿足碳化矽/碳化矽襯裡及葉片未來在1,650℃水氧耦合環境中的使用要求。其塗層結構設計如【圖1】所示,主要結構包括四層。第一層是表層耐高溫的熱障鍍膜,主要由具有低導熱率的陶瓷材料組成,包括La2Zr2O7及Gd2Zr2O7等,為下面膜層及基體提供絕熱防護,同時能夠作為第一級輻射遮罩層,以減少來自於高溫燃燒室環境及膜層高溫表面的紅外熱輻射;第二層是能量消耗層及化學阻絕層;第三層是環境阻絕層;第四層是奈米複合材料黏結層。
資料來源:Ceramic Transactions /金屬中心MII-ITIS研究團隊整理
圖1 1,650℃條件下使用的先進T/EBC設計原理
(三)高溫可磨耗密封鍍膜
隨著能源危機加劇,提高引擎效率、降低油耗成為目前航空引擎的研發焦點之一。為提高引擎效率,保護葉片與機匣不受刮擦損傷,在航空發動機氣路密封的設計與開發中導入「可磨耗」密封鍍膜,以維持最小氣路間隙而提高引擎性能。高溫可磨耗密封鍍膜用於引擎渦輪氣路密封,可減小渦輪葉片葉尖與渦輪外環之間的間隙,進而減少氣體洩漏、提高引擎效率。一般設計要求在渦輪葉片與密封鍍膜發生接觸刮擦時,膜層被刮削而葉片磨損甚小,並且摩擦係數要小,以免刮擦產生的高溫造成鍍膜或葉片燒蝕開裂,因此高溫可磨耗密封鍍膜需具有一定的減摩功能。一般來說,金屬基可磨耗密封鍍膜抗氣流沖蝕性能優良,而氧化物陶瓷基可磨耗密封鍍膜抗氣流沖蝕能力相對較差,因此在材料組成及鍍膜製備工法參數控制方面必須予以高度關注,以保證鍍膜使用壽命。
近年來,電漿噴塗MCrAlY高溫合金型(如NiCrAlY、CoCrAlY、NiCrAlYSi等)可磨耗密封鍍膜及陶瓷基(如稀土氧化物穩定ZrO2、A12O3等)可磨耗密封鍍膜獲致明顯進展,膜層可磨耗性能及抗沖蝕性能明顯提高。MCrAlY具有高溫抗氧化及抗熱腐蝕作用,一般添加聚苯酯作為造孔劑,聚苯酯加熱去除後在膜層內留下大量細小均勻分佈的孔隙可以降低膜層硬度、增加膜層可磨耗性、減輕膜層對渦輪葉片的磨損。添加六方BN或氟化物作為減摩自潤滑材料,降低摩擦係數。高溫可磨耗密封鍍膜厚度一般超過1.5mm,必須採用機器人自動噴塗技術,噴塗參數電腦閉迴路控制、鍍膜厚度線上監測,如此才能保證鍍膜組織結構及厚度的均勻性與再現性。
(四)熱噴塗陶瓷膜代替硬鉻電鍍層
因電鍍硬鉻對環境有持久的危險性,電鍍廢液中的六價鉻更是嚴重危害人體健康,減少直至取消電鍍硬鉻工法意義重大。近年來超音速火焰噴塗(High velocity oxygen fuel或High velocity air fuel,HVOF或HVAF)WC-Co、WC-Co-Cr、Cr3C2-NiCr金屬陶瓷鍍膜、電漿噴塗Cr2O3及A12O3-TiO2氧化物陶瓷鍍膜在工業上獲得廣泛應用,全面取代電鍍硬鉻工法已是必然。高速火焰噴塗WC-Co-Cr鍍膜在空巴、波音、洛克希德-馬丁等生產的先進軍/商用飛機(包括空巴A380、波音787、F-35等)已成功應用,結果顯示高速火焰噴塗的WC-Co-Cr2鍍膜在耐磨、防腐蝕、抗疲勞等關鍵性能指標明顯優於傳統硬鉻電鍍層。Cr3C2-NiCr鍍膜廣泛用於高溫摩擦磨損環境,渦輪導葉密封採用高速火焰噴塗Cr3C2-NiCr硬質鍍膜(主動磨削鍍膜)或電漿噴塗A12O3-TiO2陶瓷硬質鍍膜,具有耐蝕、高溫抗氧化、耐磨損等能力。電漿噴塗Cr2O3陶瓷硬質鍍膜在引擎密封及飛機運轉零組件磨損防護方面應用廣泛,其耐磨性及防蝕性較傳統硬鉻電鍍層提高數倍。
(五)奈米鍍膜
奈米材料技術是在1980年代誕生並仍快速發展的新技術,受到世界各國高度重視。物理氣相沉積(PVD)、化學氣相沉積(CVD)、熱噴塗、分子束磊晶(MBE)、化學沉積、電沉積等方法是獲得奈米鍍層或薄膜的典型方法。近10年來研究人員利用PVD(包括磁控濺射、離子束濺射、射頻放電離子鍍、電漿離子鍍、EB-PVD等)在製備奈米單層膜及奈米多層膜方面獲致很多成果,如奈米Ti(N,C,CN)、(V,Al,Ti、Nb、Cr)N、SiC、β-C3N4、α-Si3N4、TiN/CrN、TiN/A1N、WC-Co鍍膜可用於飛機軸類零件耐磨防蝕;電漿噴塗奈米A1203-TiO2鍍膜已用於航空引擎氣路密封;奈米Y2O3-ZrO2鍍膜已用於渦輪葉片隔熱防護;添加石墨烯、碳奈米管複合鍍膜具有雷達隱身功能。
熱噴塗是製作奈米鍍膜的極有競爭力的方法之一,與其他技術相比,具有許多優越性,如工法簡單、鍍膜材料及基體選擇範圍廣、可製備厚膜、沉積速率高、膜層成分易控制、容易形成複合功能鍍膜等,適用於大型零組件。採用奈米團聚粉末作為熱噴塗餵料,藉由嚴格控制工法參數,縮短奈米材料在焰流中的停留時間、限制原子擴散及晶粒長大,可製備奈米鍍膜。
三、未來展望
根據日本飛機協會的調查指出,由於新興國家客戶需求強勁及貨運量增加,全球商用飛機市場的年成長率為5%。與此同時,對飛機的需求亦逐年增加,預計在未來20年內將增加約兩倍。每架飛機約由300萬個零組件所組裝而成,由此可知,為滿足此一量產需求,表面處理在航空產業應用需求不可小覷。此外,根據歐盟委員會(European commission)數據,飛機排放溫室氣體,約佔全球溫室氣體4%,目前還在持續成長中。歐盟的目標是希望到2050年,飛機每公里二氧化碳排放量減少60%、氮氧化物污染減少90%、噪音減少75%。為達成此一目標,飛機製造商勢必更積極導入新興材料及關鍵零組件,而勢必將進一步推升相對應之新興表面處理技術的需求。
(本文作者為金屬中心執行產業技術基磐研究與知識服務計畫產業分析師)
全文連結:https://www.moea.gov.tw/MNS/doit/industrytech/IndustryTech.aspx?menu_id=13545&it_id=342